Tired of replacing broken wooden mats? We have the solution.
|
---|
The Development of the LastMatTM Excavation Mat.
| 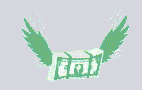 |
While planning the field operations at a
northern Ohio job site, it became apparent that hardwood timber mats would be needed as a work platform
to support a track excavator that would continuously be operated in very wet and unstable material.
The job would be a 16 hour per day/7 day per week operation, requiring constant handling of the mats, so
we wanted to be very particular with the sizing (ground pressure distribution), quality (only green hardwoods),
and assembly of the these mats. While selecting a mat company, we found there has been little or no change
in the design of mats in the past 50 years, and that most manufacturers are still sawmill companies that are
located in the southern part of the country (MS, TX, LA, FL) where hardwood trees (oak, beech, hickory) are found
in sufficient lengths and quantities.
During our first three months of operation, sixteen QUALITY hardwood timber mats were destroyed
on the job. During that same period, we purchased mats from four different QUALITY suppliers. Becoming frustrated,
we even took it upon ourselves to try a variety of modifications with some of the mats in order to achieve a longer
in-service life, but met with limited success. Something had to change. The high transportation charges and constant
labor and material costs to repair the broken mats coupled with a short in-service life were eating into the job's profits.
Something did change. Utilizing the services of a structural engineer, we sat down with a clean
piece of paper and developed LastMatTM excavation mats as an alternative to the conventional
hardwood timber mat with the following criteria in mind:
-
Utilize a type of material that would be lighter and more durable than the hardwood timber currently being used.
There are two points of contact between a track excavator and the mats: the steel tracks when
traversing the mats, and the steel edges of the bucket when handling the mats. Over a short period of time, we found
both of these repeated actions cause wood to splinter and/or crack. Additionally, most mats are designed to be used in
unstable, wet, muddy conditions. Placing them in and out of this working environment causes the wood to prematurely rot,
again shortening the life of the mat.
-
Utilize a patented one-piece construction ensuring easier, more efficient handling and eliminating connecting cables,
lifting cables or nuts and bolts that continually break on the job site no matter how careful an operator is when handling them.
-
Lastly, and most importantly, LastMatTM excavation mats had to be cost effective.
The LastMatTM excavation mat has met and exceeded our expectations of what a ground
pressure distribution mat should be. The Ohio job site has been an excellent "proving ground." A "set" of four
LastMatTM excavation mats has been in operation for over three years (double shifts/7 days per week)
with zero downtime.
If the LastMatTM excavation mat makes sense to us (and we're a company that is very hard to please),
then we're confident it will make sense to you for use in your operations. Please call us today for more details and/or to arrange to see
the LastMatTM excavation mat in working action. You may also call and request a video showing the excavation
mats in operation.
|
|